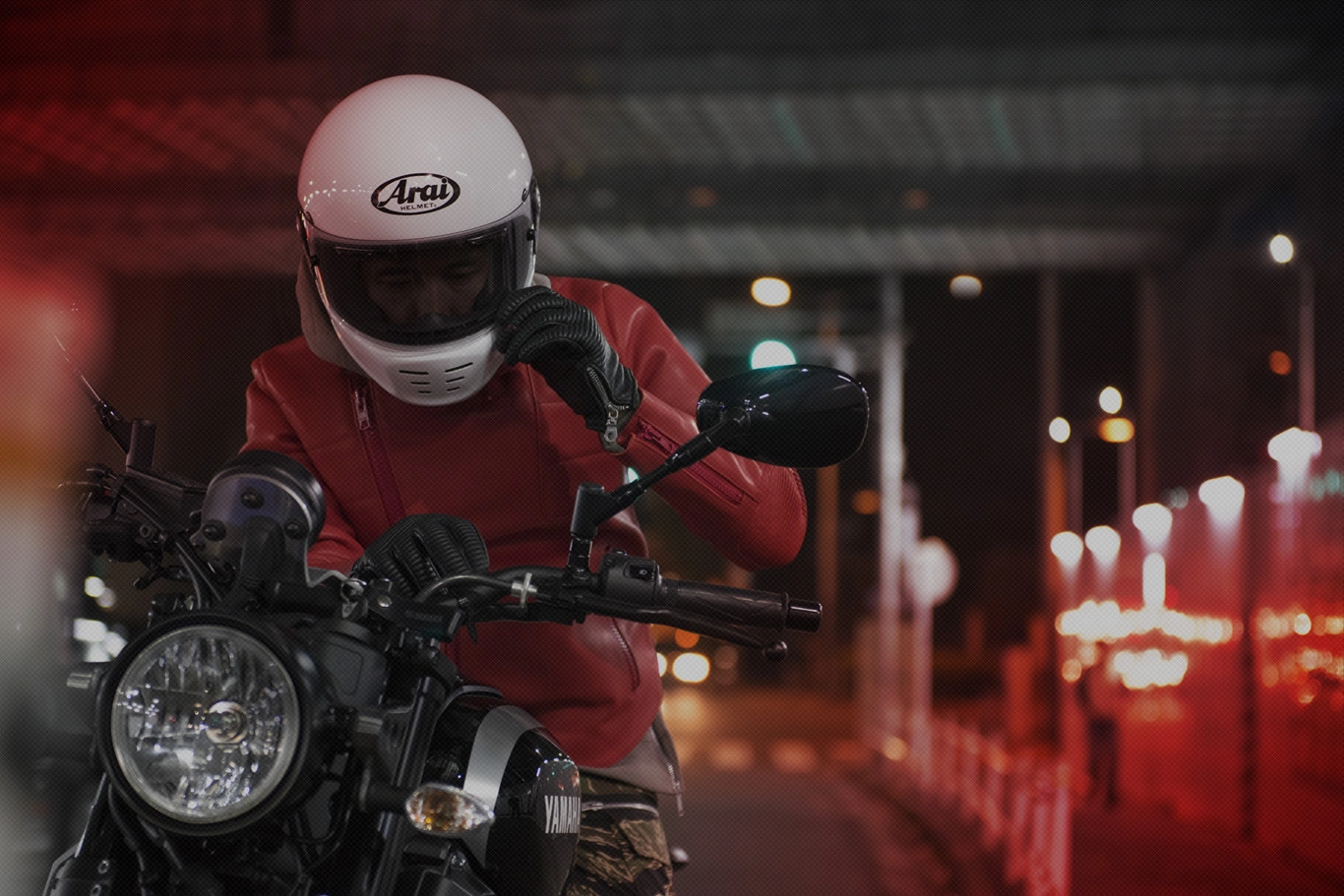
アライヘルメットとは
アライは創業当時から現在に至るまで
オーナーがライダーです。
規格のない1950年初頭から
純粋にライダーの頭を護るために
ヘルメットを作り始め、
頭を護る性能ではどこにも負けない
世界に認められるブランドを目指しました。
オーナー自らが先頭に立ち、
材料、製法、製造設備を見直し、
強靭でありながら軽いcLc構造の帽体開発に成功しました。
現在の品質管理の基礎となる全数帽体二重検査も
アライの検査員自らが帽体の責任を負うという
責任感と誇りを持って行っています。
プロテクション向上のため、
社員一同オーナーの信念に賛同し、
外から見えない部分や小さな違いを見つけて
独自の工夫を凝らす。
それがアライの違い、バリュー・オブ・アライです。

PERFORMANCEかわす性能とは
『かわす性能』とはヘルメットを滑らせることにより、
衝撃エネルギーを頭に向かわせないことです。
衝撃エネルギーを吸収する衝撃吸収性能は、
シェルの表面から頭までの限られた面積で外部からの衝撃を処理するため、
エネルギー=力×距離の公式により限界があり、
どれだけ技術が進歩しても衝撃吸収性能では守り切ることが出来ません。
また、衝撃吸収性能を司るスチロールの厚みにも限界があります。
そこでアライヘルメットは『かわす性能』に目を付けました。
1ヶ所にかかった衝撃を分散することに適した形状は球体です。
凹凸や角張った部分があるヘルメットは転倒した際に引っかかるリスクがあり、
その瞬間で更に大きな衝撃を受け、頭への衝撃だけでなく、首を捻ることによる損傷も発生します。
そういった被害を抑えるためにアライヘルメットは引っかかりがなく、段差も滑りやすい丸く、滑らかな
『かわす性能』を重点に置いたヘルメットを作り続けています。
衝撃を弱めつつ、より広い面で初撃を吸収していくことがアライヘルメットの出した『かわす性能』という結論です。
かわす性能のメカニズム
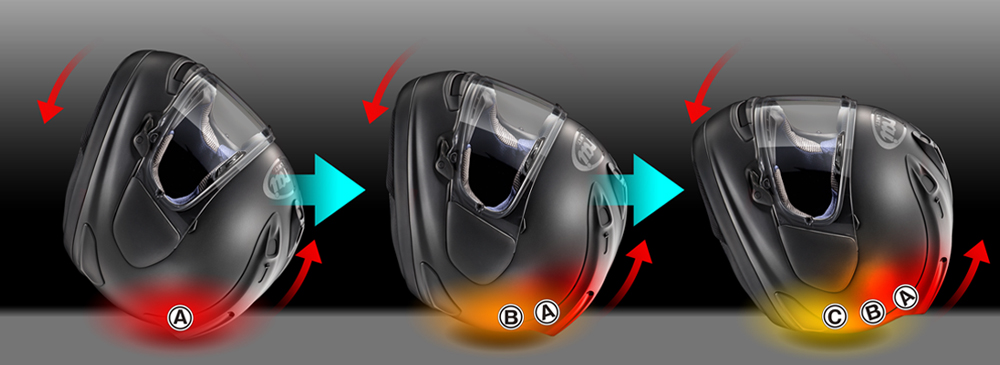
なぜ衝撃吸収性能だけでなく
『かわす性能』を重きに置いているのか
ヘルメットの耐久性や衝撃吸収性能は数値化されますが、
『かわす性能』は数値に表すことが出来ません。
定義が出来ないため安全基準には明記されておらず、性能差を確認することが出来ません。
ですが、安全基準に明記されていないからこそ、
アライヘルメットは『かわす性能』の重要性に目を付けました。
実際の転倒例や検証を積み重ねた結果、
転倒したライダーはヘルメットを滑らせることが多かったため、
かわす性能が頭を護ることにおいて重要な要素であることに気付きました。
以来、アライヘルメットは工夫や小さい改善を数十年に渡り積み重ね、
かわす性能を向上させてきました。
一つの改善で劇的に『かわす性能』が向上するという答えはありません。
衝撃吸収性能に加え、『かわす性能』の真価を
追い求め続けることがアライヘルメットの信念です。
STANDARDS規格・性能
PROCESS製造工程
01金型加工
シェルの金型はアライヘルメット創業以来、自社で製造しています。
外部に発注せず、自社で行うことによって従来であれば1週間かかる作業を
24時間で終えることが出来、
次の工程に移ることが出来ます。
自社製造により生産コストや開発時間が抑えられることにより
トライ&エラーも容易に繰り返すことが出来ます。
きめ細かく迅速な開発や改良が可能になり、デザインの自由度も高くなるのです。
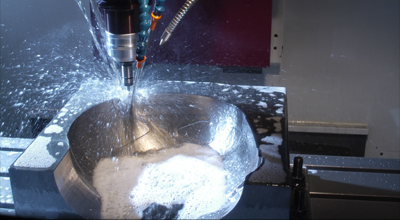
製造工程で使用する機械や試験器も自社で作られています。
02帽体成形
アライヘルメットのシェルは開口部のレーザーカット以外、全て手作業で行われています。
シェルは新樹脂配合技術により作られたスーパーファイバーにより、軽く堅牢なシェルを実現。
通常のガラス繊維の6倍のコストがかかりますが、
強度と弾性率を30%高めました。
高い融点で製造されているため、不純物も抑えています。
また、開口部には衝撃による縦方向へのクラックを防ぐスーパーファイバーベルトを使用。
頭頂部には特殊な有機繊維素材が用いられ、
頭頂部の強度を下げることなく低重心化を実現。
ネット構造で強度を高めたPB-SNC2と、それを受け継ぐPB-cLc2。
アライは軽量化に際しても強硬さへの妥協は一切しません。
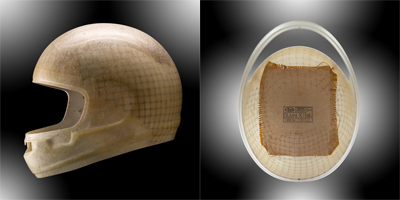
頭頂部の高強度特殊繊維により耐貫通性能を高めながら
低重心化が実現されています。
03検査
成形されたシェルは成形した本人により重量を測定されます。
その後、レーザーカットをし、成形部署内で全数厚みチェックが行われます。
成形部門で検査されたシェルは検査部門へ送られ、外観、重量、厚みの検査を再度行います。
これがアライがレースサポートを開始した当初から行われている全数帽体二重検査です。
過酷な状況下で使用されるレーサー用ヘルメットと一般のお客様がご利用されるヘルメットに
差があってはならないという思いがあり、開始されました。
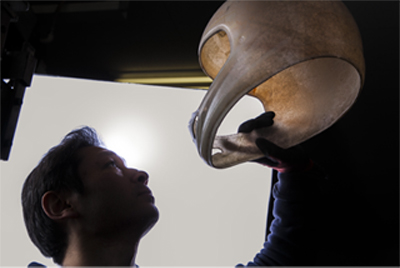
目視で判断出来るようになるまでは
何年もかかると言われています。
04下地処理
上述の通り、アライのヘルメットは一部工程を除き手作業で行われています。
塗装と転写も出来るだけ帽体に重量を載せないことを第一目標に掲げています。
FRP(繊維強化プラスチック)特有の穴は厚塗りで塗装すれば簡単に埋められますが、
アライでは軽量化を実現するためペースト状の目止め剤を刷り込み、
薄吹きのサフェーサーで塗装します。
その後、水研ぎを行い、埋まりきらなかった穴や欠けの検査をしながらパテ付けをしていきます。
ここまでの工程を2回行い、重量を測定。
少しでもオーバーした帽体に関しては修正作業が行われます。
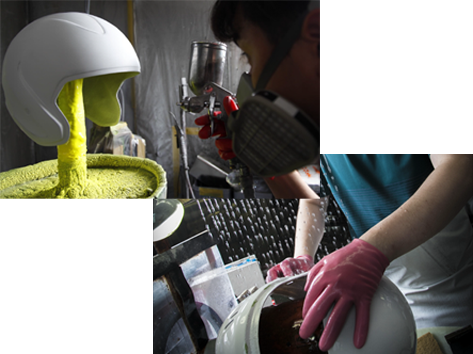
05塗装・転写
一色ずつ塗装していくマスキングデザインと、
マークを貼り付ける転写デザインの2つの方法があります。
これらの作業はもちろん完全手作業。
製品ごとに設定されているベース塗装を行い、ピンホールなどをチェック。
その後、重量を計量し、FRP製のデザイン型をもとにガイドラインを引きます。
マスキングテープも転写シートも完全手作業で貼り、ベース塗装から完成まで8、9日を要します。
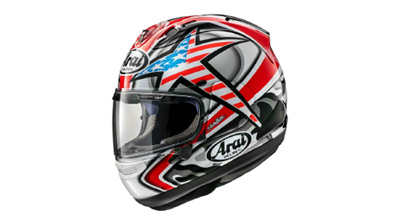
一つ一つ手作業で行われています。
06組み立て
ダクトやシールド、緩衝ライナーから首元のゴム製やビニール製の縁に巻きつけるなど、
帽体に部品を取り付ける作業です。
部品を正しい位置に取り付けることは、風切り音や風の巻き込みを抑える上で外せません。
こちらも穴あけから組み立てまで完全に手作業ですが、
失敗すると廃棄処分になるため細心の注意を払います。
失敗を防ぐために数多くのアイデア豊かなガイド類が各工程で用意されているほか、
ミスを避けるための手順を取り決めるなど工夫もされています。
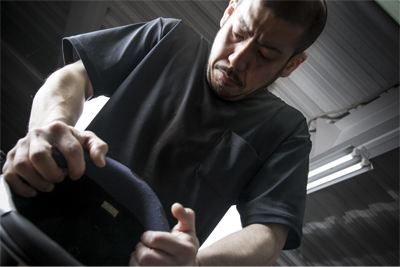
風切り音や巻き込みを防ぐため、しっかり密着させています。
07最終検査
全ての工程を終えたら最終検査に移ります。
シールドが適正に動くか、
ダクトがバランスよく付いているか、
規定の内装がついているかなどをチェック。
検査しながら、エアで細かいゴミを除去しながら帽体を磨きます。
全ての検査を終えたあと、SNELL規格品の証であるスネルラベルを貼り、全工程終了。
このような工程を経て消費者の手に渡るのです。
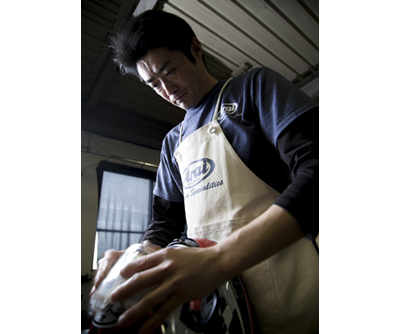
お売りするという意識を忘れません。